Computerized Maintenance Management System (CMMS Software)
ServiceTRMâ„¢
Keeping equipment up and running so tests and production meet their goals
ServiceTRMâ„¢ is used by equipment users, support groups and their management in manufacturing or engineering to coordinate preventive maintenance tasks aimed at reducing downtime, accelerating time-to-market and increasing revenue throughput. Using the onboard SupportTRMâ„¢ capability, break-fix performance is coordinated and measured enabling a continuous feedback loop used to optimize PM tasks for performance and return-on-resources.
See how Scireo software drops asset and support costs by 50% while accelerating time-to-market 2X.
Customizable escalations and notifications
Through email and text ensure the right people find out about issues quickly and efficiently.
Root-cause, correct action findings
Closed-loop process to drive improvements in preventive maintenance procedures.
Contextual data about production or engineering test schedules
It enables faster prioritization and less disruptive /lower cost coordination of tasks.
30%
Downtime Reduction
Fact-based focus on performance & obsolescence
85%
Response Time Improvement
Issue escalation and visible metrics drive ownership
15%
Reduction in Labor
New actions with high-risk assets
Increased Customer Satisfaction
Better coordination of test resources

Notable Features
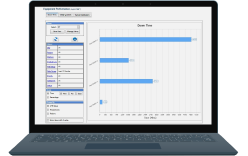
Equipment Performance Console
Used by managers aiming at reducing the downtime of their assets. Reports downtime, mean time between failure (MTBF) and Return-to-Service measures. Capable of filtering on sites, factories, platforms or specific issue categories. Like all consoles, each bar can be drilled into for access to the details driving the performance. Details are displayed on Scireo's Action Grids which are also sortable and filterable.
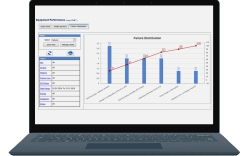
Downtime Issue Console
Used by managers aiming at reducing the downtime of their assets by reducing systemic failure issues. Each bar can be drilled into for access to specific failures within each category. Those details are displayed on Scireo's Action Grids which are also sortable and filterable.
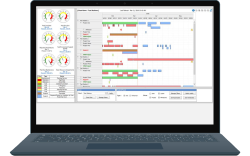
Management Console Total View
Maintenance personnel can easily schedule preventive maintenance to reduce disruption because this console provides visibility to all events scheduled to take place on your shop floor, from test event preparation to execution or production. Equipment users can easily launch a request for support from the screens they are using to manage the scheduling of their facilities and maintenance managers can see scheduled maintenance visually. This In-the-box-integration ensures the association between the specific asset down, the issue, its duration, and the specific event interrupted are available for analysis.
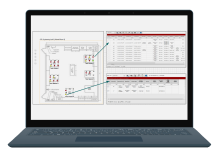
Visual Display
Our visual display can be used on a desktop or large-screen display to quickly identify and locate issues. Indicators can be inserted on facility layouts or any custom layout.
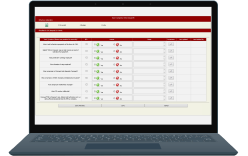
Maintenance Checklists
Our checklists are able to infinitely expand database schema quickly, without development, in a way that is available to workflows and reporting. Includes the ability to use radio buttons, pull-down menus and configure fields for dates, times/duration, and money. Users can also attach documents/schematics, images or links.
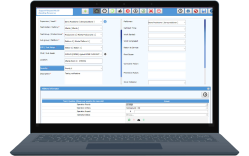
Flexible Assertions
Provides the unlimited capacity to add fields in multiple different data forms (date, number, radio button etc.) quickly and easily extending the database schema with no need for development. Data is extracted with the Flexible Analytics capability in reports that can be scheduled for distribution or exported to other systems.
Additional Capabilities
Escalations and Notifications
Create service tickets
Asset Pedigree Data
Time-based or metered maintenance
Asset Tracking
Asset Configuration/Parent-Child
Calibration Management
Inventory Controls
Mobile Access
Preventive Maintenance
Scheduling / Auto Scheduling
Service History Tracking
Technician Management
Barcoding / RFID
Work Order Management
Check-in / Check-out
Document Management
Downtime Tracking
Reason code tracking and analysis
Integration with IoT
Questions?