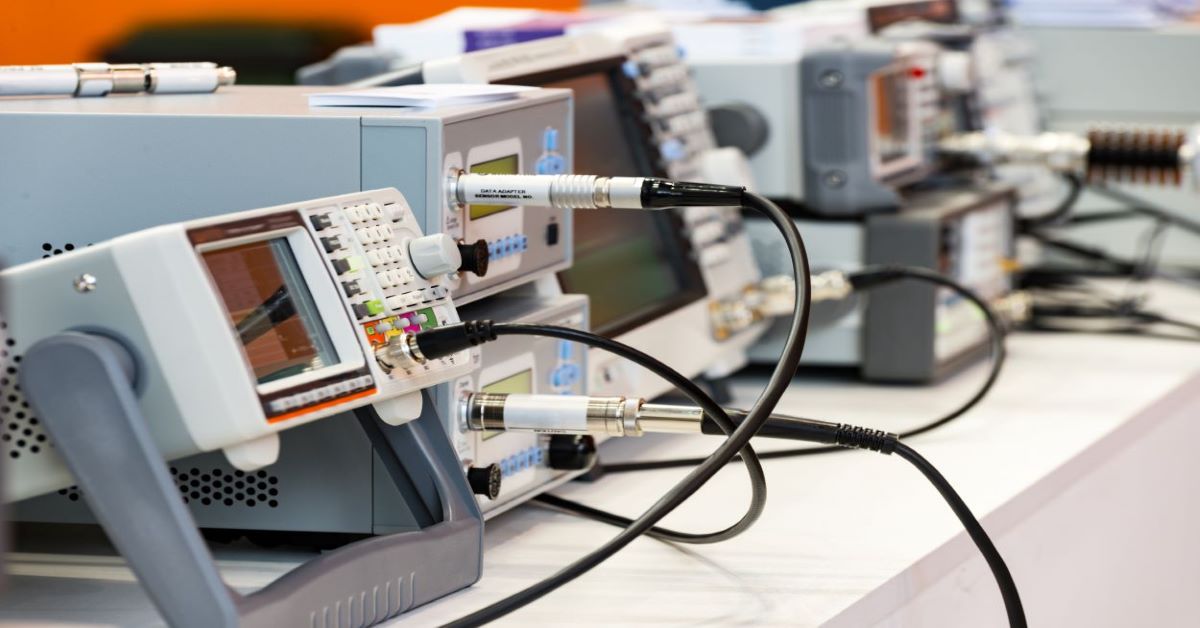

Measuring equipment utilization is the best way I know to determine if your assets are being hoarded and, as a result, if your business is incurring all of the costs associated with it. Hoarding creates the need to acquire equipment that’s not really needed and all of the support costs as well. It also causes delays and slows processes down. Solving the utilization problem requires first an understanding of why it happens and then what can be done about it. The balance of this blog post is about just that. The costs of hoarding are significant and include:
- As much as 50% to 75% increased spending on equipment
- As much as 25% to 50% increased spending on support costs like calibration and repair
- Increased labs space and equipment storage requirements
- Increased audit findings
- Asset database inaccuracies exceeding 30%
- Time wasted searching for assets, often up to 10% of an engineer’s time
Our approach and capability to improve the above performance are proven and documented by customers and industry analysts alike.
Hoarding Kills Equipment Utilization and Piles on Costs.
The genesis for founding Sente was in a conversation I had years ago with an engineering executive who was telling me he was spending way too much money on test equipment and test equipment services with my previous company. He had to somehow reduce expenditures. He told me his teams were busy and had an insatiable appetite for more equipment. The company I was with at the time was a beneficiary of this demand as we sold equipment, rented, repaired, and calibrated his equipment. The more the customers needed to buy, the better it was for us, and the rest of the test supply chain as well. None of the suppliers in the supply chain really understood the problem and, even if they did, it wasn’t in their interest to solve it.
My formal training is in engineering but I had just completed a job running a manufacturing plant where everything was about uptime, utilization, and throughput. When I asked the executive what his equipment utilization was he picked up the phone and asked a member of his staff. He reported it was 90%. When I asked how the number was calculated the response came back that 90% of assets were being used in the labs, and 10% of them were in their equipment crib. Their utilization was so high, he reasoned, because they had a process for sharing assets through the crib. The executive looked at me as if to say, “I told you so.”
I asked if we could go visit a lab because I had a hard time believing their 90% number. For that to be true the utilization in the labs had to be 100% and I knew that couldn’t be the case. It was probably lower, but how much lower I couldn’t have imagined. The executive and I visited a lab. He counted assets actively involved in sourcing or measuring. I took a tally of all of the assets in the lab. The utilization was less than 10%. Equipment utilization was the executive’s biggest problem. It was driving significant costs. I didn’t know what was causing the problem, but I knew we were on to something.
A fundamental Mechanism Drives Equipment Utilization
The more companies I visited the more the numbers came back within a very tight range: 7% and 15%. There was some sort of “physics” at play that made each company, as different as they were, the same when it came to utilization. Luckily I had been studying economics, organizational design, cognitive science, and systems thinking and was able to discern the mechanism at work was the “tragedy of the commons.” When a fixed resource is shared by a community people wind up trying to hoard the resource so they can be sure they get their share of it. It is the mechanism that most famously leads to overfishing of areas like cannery row in Monterey, California. It’s what leads to hoarding test equipment or services and then the subsequent need to have more equipment and services than would be necessary if hoarding didn’t exist.
Low equipment utilization is caused by hoarding. This was our challenge and it is one we’ve solved for our customers over and over again. Our solution is not a “common sense” solution though. It is was companies would have figured it out on their own. We still find equipment utilization issues exist broadly across the marketplace.
Why Act Now to Increase Equipment Utilization?
Because we are in the most competitive marketplace in human history and our companies need to transform to move with more speed and lower costs if we want to compete effectively.
Higher test equipment utilization levels allow companies to unleash existing, pent-up investment capital capacity. Management then has the flexibility to shift already-planned investments of capital to new areas or hold on to newly released capital capacity for future programs while dropping the savings directly to the bottom line as a cost reduction.
Increasing utilization is also essential when it comes to maximizing the time of engineering personnel. An effective test environment management program improves the utilization of engineering capacity by minimizing or eliminating the need for engineers to be distracted by administrative concerns related to test equipment.
Low utilization can also be a symptom of something far more damaging: the distrust between your teams that leads to hoarding is also the distrust that will put the breaks on speed, innovation, and growth as we discuss in the blog post Are You Building a Foundation for Speed?
Do you have a hoarding and utilization problem? What is your number? Get the answer by working with Sente to Uncover Opportunities for Improvement.
Request a Demo
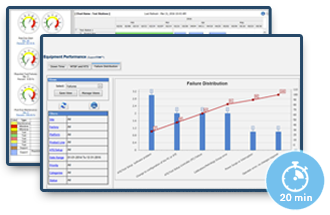
See how Scireo aEAM Software drops asset and support costs by 50% while accelerating time-to-market 2X.
Relevant Content
Virtualizing aEAM Feasibility, Planning & Install: Faster, Lower Cost, Accelerated Results
aEAM (Accelerated Enterprise Asset Management) achieves 2X to 4X improvements to asset utilization, throughput, and speed compared with typical asset management solutions. You can now launch twice as fast getting results in 30 to 60 days! Great projects have great potential and get key constituents on board to drive the change with the knowledge and…
Unlock Hidden M&A Synergies in Test Infrastructure
Why are There Hidden M&A Synergies in Test Operations? Our customers often make the decision to focus on synergies in organizations heavily invested in test because of the capital intensity — both human and equipment — in test organizations. The synergies come later than that have to though, as our algorithms could also help M&A…
Equipment Utilization Case Study: Space Company Leverages Assets
The hoarding culture was slowing this company down while impacting cost and quality. See how a journey to common processes and collaboration lead to a 50% reduction in assets as their business doubled.
Case Study: Leading Defense Manufacturer Drives Asset Reduction
See how a Blueprint-for-Action baselined their situation and rapidly installed Scireo suite. It enabled a 50% reduction in obsolete equipment, provided equipment for their growing workforce and solved their compliance challenges.
Notable Quotes
“Test Resource Management has been instrumental in changing the mindset of engineering to think in terms of sharing the test equipment, and treating the test environment as a business within a business,”
– Director of Engineering, Fortune 75 Company